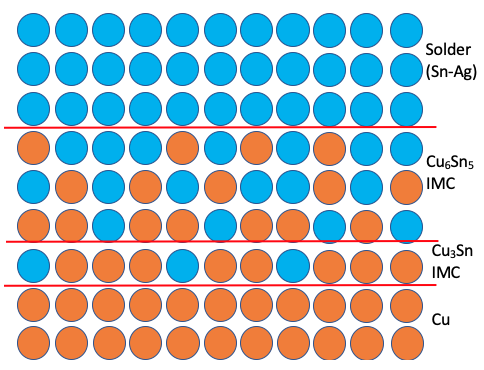
Soldering is a joining process used to join metal with an alloy material that has lower melting temperature than the joining metal with the application of heat.
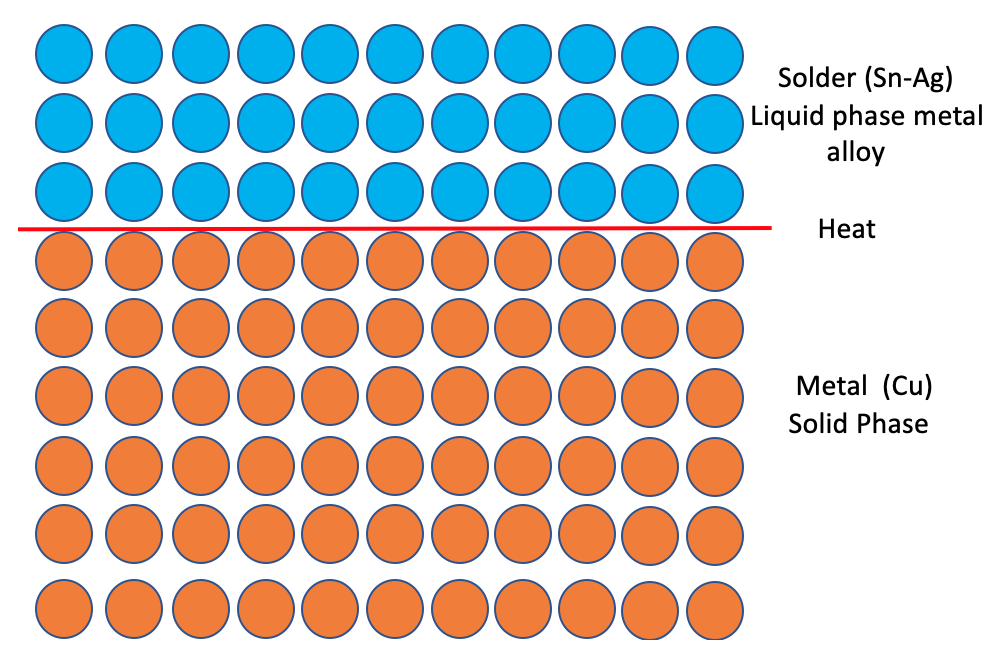
- Three main components in soldering: a) Molten alloy should be able to wet both the joining metal surfaces b) Gap between the joints must be filled with the solder alloy c) After solidifying, the solder must form a permanent bond of intermetallic compound (IMC) between the mating surfaces.
- Solder joints provides mechanical, electrical and thermal connection between the connecting surfaces, such as between the dies & substrate or PCB in the IC packaging.
- The solder joint must withstand the thermo-mechanical as well as electrical stress induced by CTE mismatch between the components and operating conditions extremes such as higher power and higher temperature.
- Solderability is the ability of the material to be wetted by the molten solder such that it adheres well on the metal surfaces.
- Typically, metal surfaces will have native oxides on its surfaces and flux is applied to the metal surface to remove those oxides before solder application. Flux protects surface from oxidation during heat treatment & it floats out remaining oxides on top of the molten solder. Flux also promotes wetting action of molten solder by lowering its surface tension.
- Flux types : No clean flux – residues not cleaned & is benign, Water soluble flux – requires a wash after reflow, Saponifier – wetting agent used in the wash cycle.
- Flux can be : Rosin fluxes- RA active or RMA mildly active, Resin flux, Organic flux and Inorganic flux.
- Flux activity level classification : L0 – 0% Halogens, L1 – <0.5% , M0 – 0% Halogens, M1 – (0.5% – 2%) Halogens, H0 – 0% Halogens, H1 >2% Halogens.
- Solder paste is primarily composed of solder powder (balls), flux (acids), binders, activators, tacky paste and is dispensed using canisters, syringes, paste pumps etc.
- Typical solders in use are either Tin Lead (SnPb) or Lead free solder. Lead based solders are mostly phased out as part of RoHS (Restriction of Hazardous Substances) directive in electrical and electronic equipment.
- Tin Lead solder is 63/37 alloy composition of Sn/Pb and is eutectic (sharp melting point – 183°C) with peak reflow of 210°C – 230°C.
- Lead free solder is the workhorse of today’s solder material in which Lead in Tin Lead solder is replaced with Silver (Ag) & Copper (Cu) and is called SAC alloy (Sn/Ag/Cu).
- In addition to the several SAC alloys in use such as SAC125 (Ag-1.2%, Cu – 0.5%, Sn – balance), SAC305 (Ag- 3.0%, Cu – 0.5%, Sn – balance), SAC405 (Ag-4.0%, Cu – 0.5%, Sn – balance), Sn/Ag and Sn/Cu are also in use for niche applications. Lead free solder melting point is – 217°C and reflow temperature is 235°C-245°C with the maximum of 260°C.
- High silver (>3%) SAC alloys exhibits poor drop shock performance.
- Solder pastes are made with variety of powder size mainly as type 3, 4, 5 & 6. Type 4, 5 & 6 are increasingly finer in size and allows to print miniature components and smaller stencil apertures. However surface area of finer powder type is significantly higher than the larger solder powder type and reacts faster. The fast rate of reaction can be problematic in some instances that prohibits the use of finer types of solder paste.
- Lower wetting angle provides greater surface area coverage by the solder alloys and provides higher adhesion for solderability.
- On the contrary, higher wetting angle will have lower surface area coverage by the solder alloys and has higher cohesive force yielding poor solderability.
- The shape of solder on the metal surface depicts a truncated sphere. The more the sphere that gets distorted or less of the sphere that is visible, the higher the wetting of the surface for better solderability.
- In terms of contact angle, lower contact angle of the alloys will provide better wetting and thus the solderability. 0° contact angle is complete wetting of the surface, 0° to 90° indicates the solid surface is wettable and contact angle above 90° indicates the solid surface is not wettable.
- The key to good and reliable solder joint is formation of an IMC at the interface. The IMC is formed due to the diffusion of dissimilar atoms at the interface which holds everything together. The IMC should not be too thick, too granular and should be free of any kirkendall voids.
- Metallic diffusion process depends on temperature & time. Higher temperature and longer time results in higher diffusion process and thus thicker IMC layer.
- Reflow profile is critical part of the soldering and overall package assembly process and primarily divided into – Pre Heat Zone, Soak Zone, Reflow (Peak) Zone and Cool Down Zone.
- Reflow profile critical points definitions: RAMP – is change in temperature over time in which slope of the temperature vs time curve changes to 2-4° C/sec. Higher ramp rate causes rapid evaporation of the flux in the solder paste resulting in lifted leads, solder balling and tombstoning. SOAK – is a solder paste phase change process in which all components and PCB board will reach into equilibrium. Too slow of the soak process will have higher flux concentration impacting poor wettability resulting in voids, cold solder joints etc. TAL (Time Above Liquids) – phase changes in the solder paste and reflow is initiated. PEAK – The further increase in temperature over liquidus ensures that the high density areas in the package will also gets proper and complete reflow. COOLING – This is a failing slope and should not exceed 6°C/sec as some packages are sensitive to the higher rate of cooling.
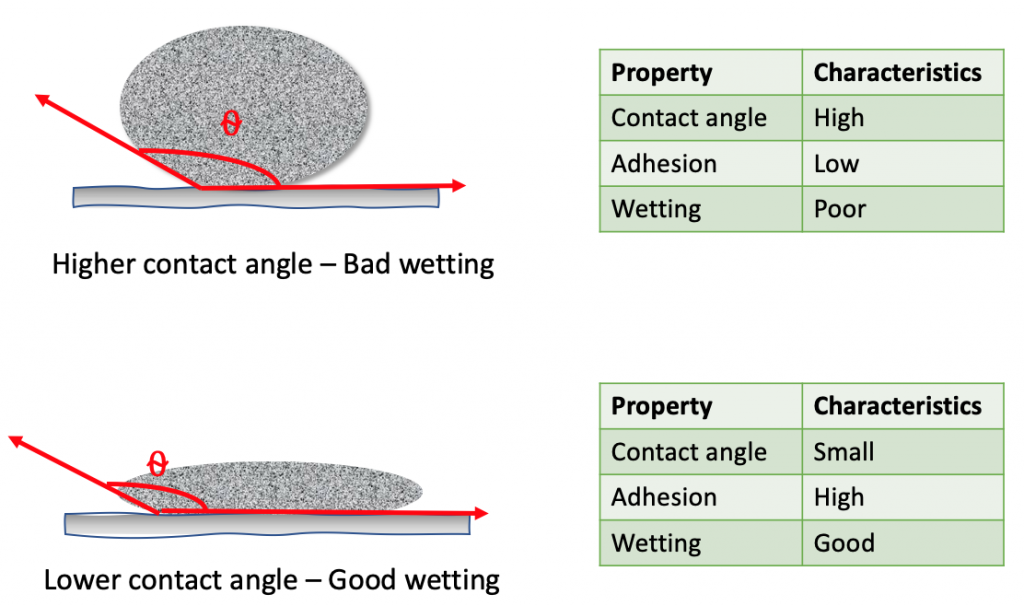
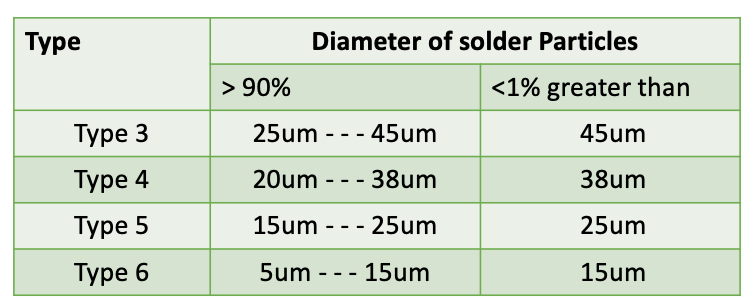
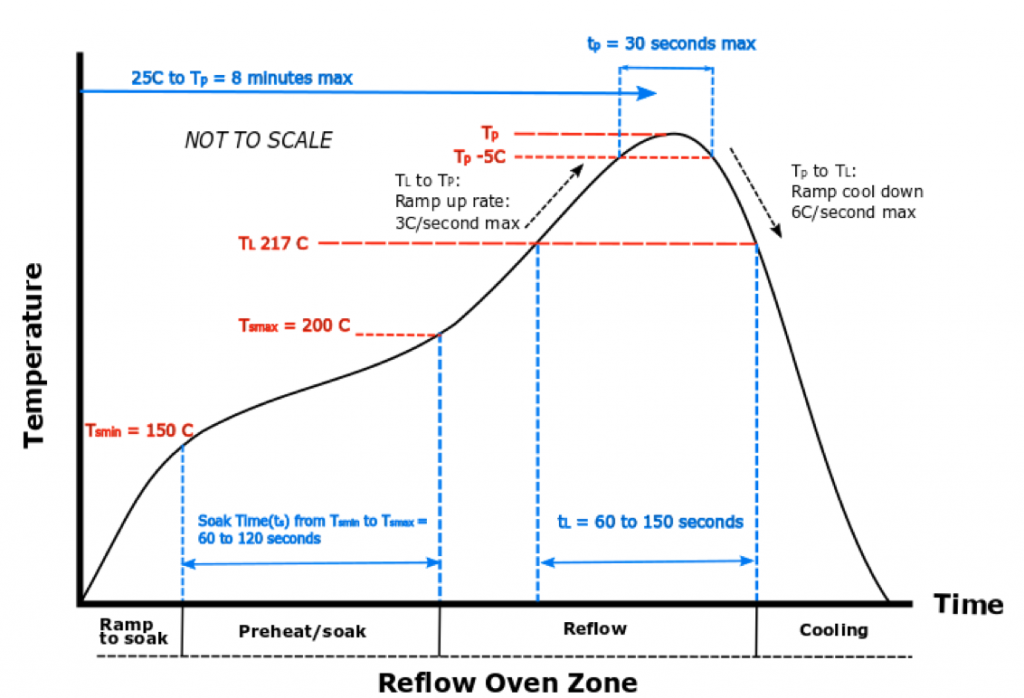
RSS
engage